Production Quality Control
For $290
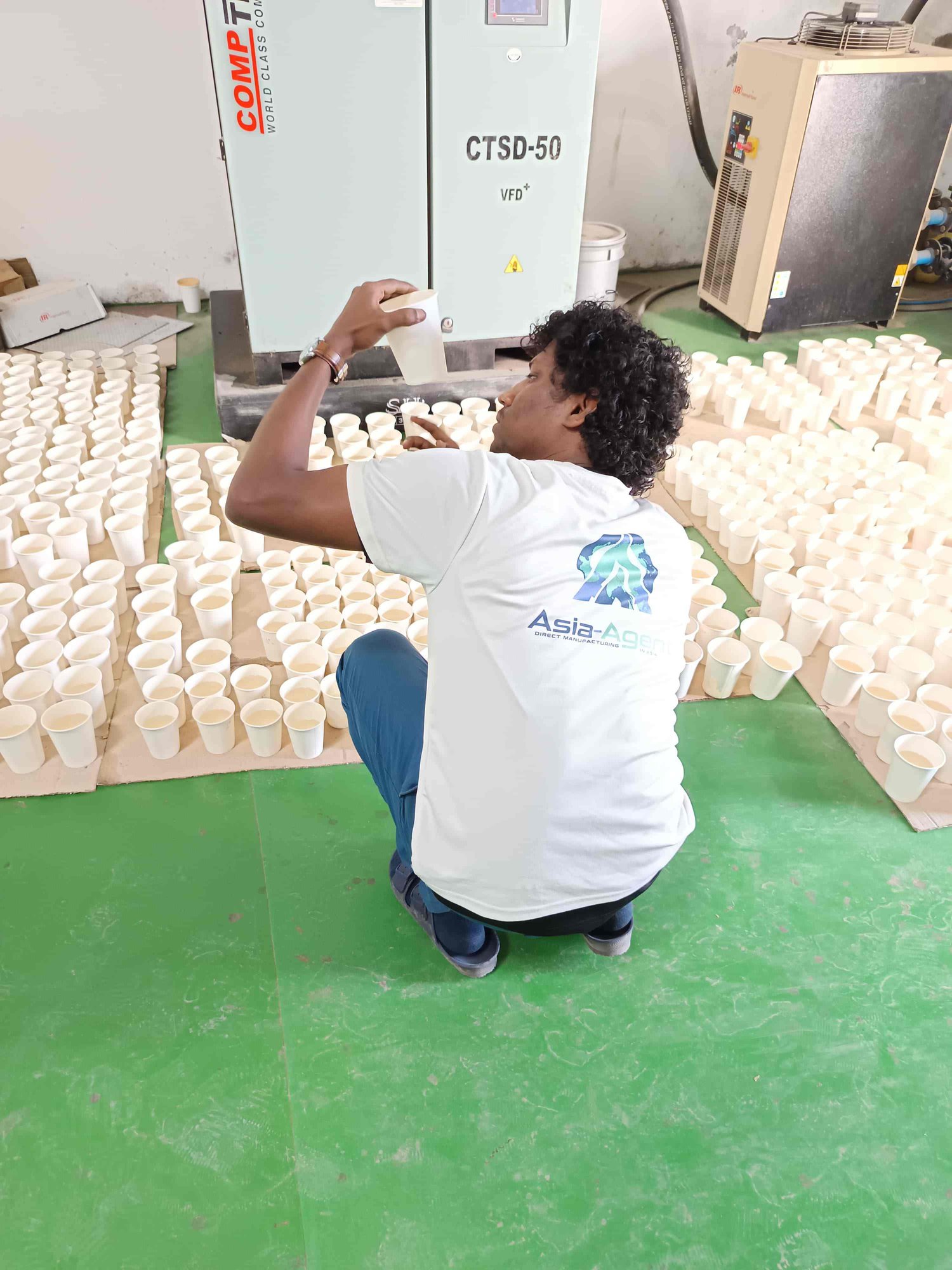
Catch Quality Issues Early & Ensure Your Order Meets Standards
Without proper oversight, factories often cut corners during production, leading to defective products, misaligned specifications, and shipment delays. A Production Quality Control (Simple Visit) ensures your order is being manufactured correctly before it leaves the factory, reducing the risk of costly surprises.
Why This Service Matters
- Prevent Shipping Defects – Identify defective units, incorrect packaging, and substandard materials before shipment.
- Confirm Production Progress – Ensure your order is on schedule and that the factory is following agreed specifications.
- Avoid Costly Returns – Catch quality issues before the goods are shipped, saving you money on returns and customer complaints.
- Independent Inspection – Get an unbiased, professional quality check, instead of relying on factory self-reporting.
What’s Included in This Service?
1. Random Sample Inspection
- Selects a random batch of products for visual and functional testing.
- Identifies defects, inconsistencies, or material changes that may have occurred during production.
2. Quantity & Packaging Verification
- Confirms the correct number of units are being produced and packaged.
- Checks for missing parts, incorrect labeling, and improper packaging that could affect shipping.
3. Basic Defect Identification
- Examines products for cosmetic, structural, and functional defects.
- Highlights potential quality issues that may affect performance, durability, or safety.
4. Photo & Video Report
- Provides detailed images and videos of inspected products, packaging, and production conditions.
- Includes a summary of findings, defects (if any), and recommendations for corrective action.
Deliverables
- On-Site Factory Inspection – A physical quality check during or after production.
- Inspection Report – A detailed summary of product quality, defects, and overall production status.
- Photo & Video Documentation – High-resolution images and videos from the factory floor.
Pricing
$290 per inspection
For multiple inspections or ongoing quality control, contact us for a custom package.
How It Works
- Submit Your Request – Provide factory details and production timeline.
- Asia Agent Conducts the Inspection – Our expert team visits the factory and inspects production.
- Receive Your Quality Report – Get a full breakdown of findings, including photos and videos.
- Take Action – Decide whether to proceed with shipment, request corrections, or escalate issues.
Understand all details before choosing the Production Quality Control service.
Discover how our Production Quality Control can transform your manufacturing approach and offer you the edge you've been looking for.
Production Quality Control (Simple Visit) is a one-time factory inspection designed to ensure your order meets the agreed specifications before it is shipped. This service helps businesses detect defects, confirm order quantities, verify packaging, and prevent costly returns or customer complaints. Without proper quality control, suppliers may cut corners, use inferior materials, or ship defective products.
Our inspection identifies common manufacturing defects, including:
- Surface Defects – Scratches, dents, color inconsistencies, poor finishes.
- Structural Defects – Warping, loose components, incorrect assembly.
- Functional Defects – Non-working electronics, faulty hinges, poor stitching, battery malfunctions.
- Material Substitutions – Use of lower-quality or incorrect materials compared to agreed specifications.
If critical defects are found, we provide recommendations for corrective action before shipping.
Suppliers may use cheaper materials, reduce product quality, or outsource production without informing buyers. Our on-site inspection verifies that your products are manufactured according to agreed specifications, preventing fraudulent practices such as product swaps, counterfeiting, and quality downgrades.
We follow industry-standard random sampling methods, inspecting a representative batch from the total production lot. If you need an AQL (Acceptable Quality Level) statistical sample or a larger percentage of units checked, we can adjust the sample size based on your specific requirements.
If defects are found, you will receive a detailed report with photos, videos, and issue breakdowns. Based on the severity of defects, you can:
- Ask the supplier to rework or fix the defective units before shipment.
- Negotiate compensation or discounts based on the quality issues.
- Decide to reject the shipment if defects exceed acceptable limits.
Our team can assist with supplier negotiations to resolve quality disputes.
Yes, we perform basic functionality tests based on the product type, such as:
- Powering on electronic devices.
- Checking buttons, zippers, hinges, or moving parts.
- Testing battery performance (for applicable products).
If you require in-depth performance testing or lab certification (e.g., CE, FCC, RoHS, REACH, ASTM standards), we offer separate compliance testing services.
Yes, our quality control visit includes quantity verification to confirm that:
- The supplier is producing the correct number of units.
- There are no missing components or underproduction issues.
- Packaging and labeling match order requirements.
This prevents issues where suppliers short-ship or mislabel orders, which can cause import clearance problems.
Pre-Shipment Inspection (PSI) is conducted when 100% of the order is completed and ready for shipment, whereas the Production Quality Control (Simple Visit) can be done during or after production to catch defects early. If you need a final pre-shipment check, we can arrange a PSI as a separate service.
Yes! Many buyers combine this service with our Pre-Production Readiness Check to ensure quality control at multiple stages:
- Before production – Verify materials, machines, and workforce readiness.
- During production – Catch quality issues early before full production is completed.
- Before shipment – Perform final checks to prevent defective goods from being exported.
This multi-step quality control strategy minimizes risks and ensures consistent product quality.
This basic quality control visit does not include full compliance verification. However, if you need:
- PFAS, REACH, RoHS, or Prop 65 chemical testing.
- Material traceability checks.
- ISO, BSCI, or other certification verification.
We offer separate Factory Compliance & Certification services tailored to your industry’s regulatory needs.
The most frequent quality control failures include:
- Incorrect materials or missing components.
- Cosmetic damage, paint inconsistencies, poor stitching, or rough finishes.
- Electronic defects (e.g., failure to power on, loose wiring).
- Packaging issues (wrong labels, poor sealing, incorrect dimensions).
- Factories rushing production, leading to high defect rates.
By conducting early quality control visits, we help brands avoid receiving defective goods that lead to customer complaints, refunds, and bad reviews.
- The Production Quality Control (Simple Visit) costs $290 per inspection.
- We provide this service in Vietnam, India, China, Indonesia, and Bangladesh.
- If you require multiple inspections or an ongoing QC program, we can provide customized pricing based on your needs.
If a supplier refuses quality control visits, this is a major red flag. It may indicate they:
- Are hiding defects or production problems.
- Are not the actual manufacturer and are outsourcing orders elsewhere.
- Are not operating transparently, which could lead to disputes or fraud.
In this case, we recommend:
- Negotiating inspection as part of your supplier contract.
- Reevaluating the supplier’s reliability and sourcing alternatives.
Simply contact us with your factory details and production schedule. We typically conduct inspections within 5-7 business days, depending on location.
Your Manufacturing Revolution Begins Here
step beyond the conventional. With our unique blend of local insights, comprehensive evaluations, and cutting-edge market intelligence, you're not just adapting to change—you're driving it. Contact us today to transform these insights into your strategic advantage. Let's redefine what's possible together.
Contact Us
Starting with a free feasibility test, we like to kick things off on the right foot. It's our way of showing you what's possible without any commitment—just honest, straightforward advice aimed at making your manufacturing journey more affordable and reliable.